Business and production environments are always evolving. The most successful companies stay closely attuned to the ongoing changes and develop creative strategies to respond accordingly.
Such was recently the case for Symcor, one of Canada’s leading providers of business-processing and communications-management services for major financial, insurance, retail, and telecommunications companies.
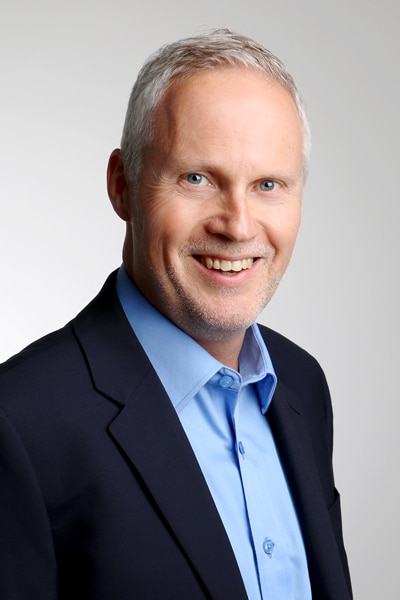
The company was facing a pending lease expiry in Montreal at its 80,000-square-foot payment-processing facility at a time when the city’s real estate market was very tight. The situation made it difficult to find new space that was cost-effective, conveniently located, and compatible with the company’s operational needs.
At the same time, Symcor was experiencing overall business fluctuations, including in production volumes at 650 Bridge Street, its 50,000-square-foot facility that handles work for its print and insertion clients. The alignment of the two circumstances presented the opportunity to merge the two business units, reduce the company’s overall footprint and expenses in Montreal, and leverage other operational and HR benefits.
Tim Hocking, Symcor’s vice president of real estate and facilities, helped lead the consolidation, which included working closely with the landlord at 650 Bridge Street, who had additional appropriate space available at 654 Bridge Street, approximately 10 meters away.
“There are usually property managers and third-party brokers involved in negotiating a lease agreement,” Hocking says. “But, considering we were one of the first anchor tenants when the Bridge Street location was initially developed, we leveraged our strong personal relationship with Fadi Melki at Carpet Art Deco [the landlord] to negotiate the relocation of the adjacent tenant and prepare the space.”
The consolidation of Symcor’s Montreal facilities reduced their combined footprint by 48,000 square feet and saved approximately $2.4 million in occupancy costs annually, but there were some challenges along the way. Planning for the relocation began twelve months ahead of time, and Hocking says the total number of employees and the business volume that had to be accommodated during that period was rather “fluid.” Symcor’s real estate and facility teams collaborated with the operational business leads, technology partners, EPO, and other internal and external stakeholders to develop appropriate solutions, functioning as a single, closely aligned unit to address the complex requirements of daily operations. Among other strategies, they set schedules and routines for incoming data and supplies to meet predetermined time frames for various projects, ensured compliance with the necessary security configurations, and made sure that electrical infrastructure was sized correctly for new equipment and that particular departments were placed in appropriate proximity to one another.
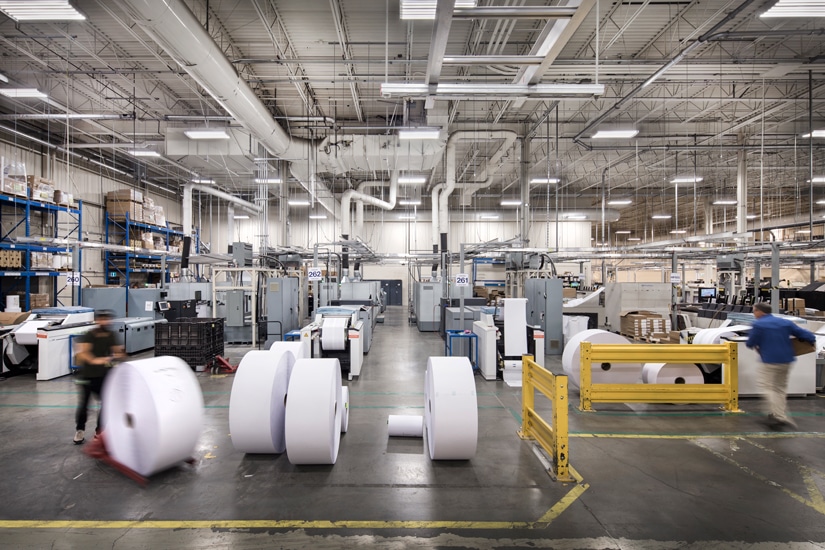
“We’ve all worked together for a long time and understand what’s required to keep operations running smoothly,” Hocking says. “Even a small, unaccounted-for change might affect the storage requirements for incoming cartons or even the dock configuration itself, which can interfere with successfully meeting deadlines and being up and running around the clock.”
Once on-site at the new location, there were additional subtleties that had to be adjusted, including balancing human-comfort factors with the requirements of a production environment. For example, adjustments had to be made to the facility’s air flow because high-volume movement was initially causing paper jams during printing processes.
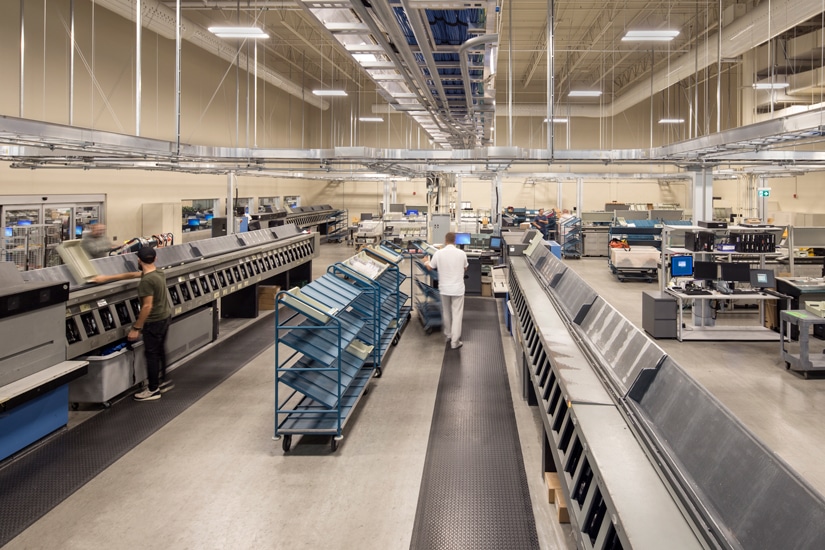
Otherwise, the facilities merger has produced noticeable benefits. It has reduced personnel redundancies and improved the effectiveness and consistency of company communications. Remote monitoring of an extensive security network of access control points, close-circuit video, and temperature- and power-monitoring sensors is saving approximately $200,000 annually. And, the space is also designed to be responsive to changing business volumes and requirements, allowing for the seamless integration of new clients and production projects.
Because of the merged facility’s configuration and the new culture of “one team under one roof,” there have also been increased levels of cooperation across all departments. “We’re all better aligned with company objectives,” says Robert Gagne, Symcor’s general manager in Montreal. “When there are heavier volumes in one area, everyone who’s available from other areas is ready to roll up their sleeves to help get work out the door.”
The company has since implemented similar consolidations at three other locations across Canada. Along the way, Hocking has learned that the more communication there is to prepare personnel to know what to expect, the better. “This blended model of developing more flexible industrial environments is definitely becoming the norm for any future site opportunities,” he says. “But, it’s still a continuous learning curve.”