Getting your Trinity Audio player ready...
|
Core-Mark International, a Fortune 500 company and leading distributor of fresh food and packaged goods to the convenience retail industry across the United States and Canada, embarked on an ambitious expansion of its in-house technology in 2016. Since then, it’s implemented many improvements—but only in certain aspects of its operations and only at select locations.
It might seem like a scattershot approach, but everything is precisely aimed.
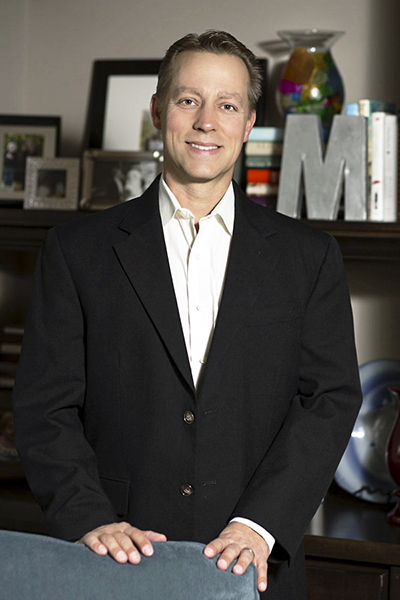
For example, Core-Mark’s new headquarters facility in the Dallas/Fort Worth area features increased analytics capabilities tied into its new “center of excellence.” The accumulated data will help the company better understand its customers’ needs as well as industry trends. But it can be a significant educational tool as well. “We intend to let our customers come to the center and ‘deep dive’ into that data,” says Charles Morse, senior director of facilities and planning. “It will demonstrate how Core-Mark can help them be more successful.”
The company’s warehouses benefit from upgraded electrical control and monitoring systems. “Each facility has numerous refrigerated spaces, and maintaining the correct temperatures is expensive,” the senior director notes. “By using them more efficiently, we reduce those costs and help extend the life of the asset.”
Other systems provide a sort of “chain of custody” from products moving through the warehouse. “We can now better track, monitor, and document the time products come in, their arrival temperature, and their shipping temperature. It helps guarantee that merchandise has been properly handled,” Morse says.
Additionally, diagnostic systems alert maintenance personnel to developing issues before they become major problems. Other hardware/software manages the HVAC system, lighting, and even daily electricity use. Morse mentions that in California, companies can get a rebate for participating in an off-peak program that lowers electrical bills simultaneously.
Core-Mark has also improved its on-floor automation. “Overall, we’ve automated 20 to 25 percent of our operations,” the senior director says. “But one of our key challenges is staying nimble. Our customer base and its demands change every few years—terms of contracts can vary from short to long—and we need to respond to those changes. For example, one of our facilities might have two customers that make up 30 percent of its volume. If one of them leaves, or another major customer comes on board, the dynamics can shift significantly.”
The improvements are geared toward greater efficiency and employee safety and productivity.
Core-Mark’s newest innovation is a multi-shuttle system that transports merchandise in prepacked totes with less manual labor than before. “Our old system required manual sorting and segregating of customer codes, packing the totes, consolidating the orders, palletizing them, and then loading onto trucks,” Morse says, while the new system gets the totes to their destinations quickly and smoothly.
“We are piloting an automated guided vehicle (AGV) program,” he adds. “Because AGVs operate without human control, they can independently transport material from point-to-point, freeing employees for other necessary work.”
Core-Mark has also improved the safe usage of its powered industrial trucks. “We now track whether a driver is actually certified to use the vehicle before releasing it. If there’s an accident or the truck is misused, an auto-stop circuit keeps the truck from moving until a supervisor checks it out. And we can track usage metrics—how often and how long the trucks are moving, idling, and actually working,” Morse explains.
Order picking is still done manually, but Core-Mark coordinates it via “voice picking.” Workers wear a headset and receive verbal instructions about the product needed, its location, and quantity for a given order. The senior director notes that workers previously used bulky radio frequency guns or paper lists, but the hands-free voice-pick gear provides greater mobility.
Additional improvements include a variety of devices and equipment to increase worker safety, such as sensor-driven lights that warn of oncoming material-handling vehicles. “They alert truck drivers, loaders on our docks, and so on,” Morse explains. “During the workday, the floor sees lots of activity, and these systems help keep everyone safe.”
Automation sometimes leads to workforce reductions, but Core-Mark’s approach is actually employee-centric. “We strive to be strategic with our labor force,” Morse says, “and automation has reduced the need for them to engage in repetitive or physically demanding tasks. We’ve found that injuries from stress or fatigue have decreased, and we meet or exceed our key performance indicators. In fact, our facilities have achieved productivity increases 2 and 3 percent.”
Part of Morse’s responsibilities in Core-Mark’s five-year strategic plan includes setting objectives for different technologies in particular areas of the operation, then testing and evaluating new products and systems to determine which are most suitable for the company’s needs.
And while it will continue to be an incremental process, “It’s better than trying to make a giant leap upward that you really aren’t prepared to do,” Morse concludes.