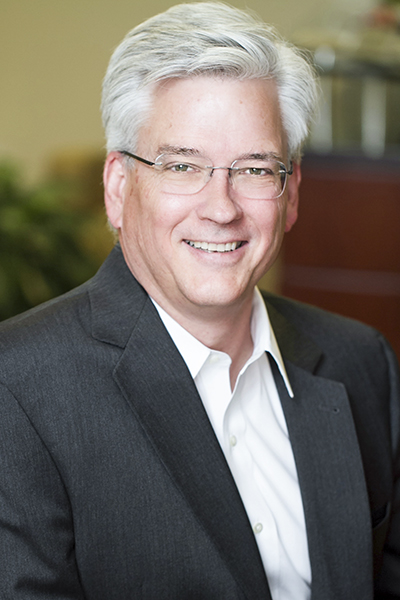
Naval ships are basically small cities that people don’t leave for weeks or months at a time. They provide living quarters for sailors, serve meals, run power generators and propulsion systems, handle sewage, and carry cargo and weapons. Unlike cities, though, they must endure some of the harshest environments and conditions, including corrosive seawater and violent storms and swells. And, they’re designed for war.
Bruce Samuelsen, COO of Alion Science and Technology and president of Alion’s international subsidiaries, has been working on the design of naval and commercial ships his entire 35-year career. He says such long stints are common among the engineers and naval architects he works with because it can take 10 years to build a ship, and the overall life of a ship can exceed 30 years or more. This long lifespan impacts the relationship Alion has with its customers, which can also last 30 years or more.
Two project areas Samuelsen’s been involved with in his time illustrate the complexity of naval shipbuilding—and the advancements being made to contain costs while ensuring a strong defense.
Floating Supply Ships
Alion doesn’t build naval ships. It partners with the ships’ owners and operators—navies, most often—providing strategies, designs, transition to production, problem-solving, and construction oversight of the thousands of pieces of equipment, parts, and components that go into each vessel. The company has assisted with the design, construction, and operation of warships for naval fleets around the world, familiar in cinema and real life, particularly in naval port cities such as San Diego, California; Honolulu, Hawaii; and Norfolk, Virginia.
But, lesser known to civilians are underway-replenishment (UNREP) ships. These ships are vital to naval operations because they are used to transfer supplies and personnel between oceangoing vessels, given that it’s not always practical to go to port for such functions.
“While at sea, there is need for all kinds of replenishment,” Samuelsen says. “That includes fuel, water, food, spare parts, and munitions. It also includes removing things like trash.” It’s a heart-stopping operation to observe, with suspended fuel lines, held up by load-bearing wires and fed into a receiving bell, stretched about 30 yards between the two ships in motion, traveling at the same speed (between 6 and 16 knots) yet affected by swells of up to two meters. The operation carries inherent risk as both ships have to maintain a precisely fixed speed and direction over the time it takes to execute the transfer.

Samuelsen is quick to point out the idea of UNREP ships isn’t new but that Alion has undertaken engineering analyses to devise better ways of managing storage, supplies, and transfers. This application of engineering techniques within the ship-design process is critical to optimizing overall ship performance. “We’ve recently had an evolution of ship elevators,” he adds, which was a direct outcome of industrial engineering analysis of the material throughput requirements.
UNREP ships have been around long enough that back in the 19th century, the famed British Royal Navy depended on “coaling stations,” which were part of the empire’s global logistics network. Experimentation was then conducted by both the British and US navies, and the work accelerated with the start of World War I. Today, Alion helps design and acquire UNREP ships for the US Navy and the Royal Canadian Navy, which are 690 feet and 560 feet in length, respectively. These are actually larger than most of the ships Alion services; destroyers are slightly smaller, but aircraft carriers are about 1,100 feet in length.
With UNREP and other types of ships, there is growing excitement around two technological advancements: all-electric ships, which carry their own energy storage in place of internal combustion engines, and autonomous (self-driving) ships.
The Canadian Surface Combatant
With the enormous costs involved in naval shipbuilding—the USS Gerald Ford, one of the largest aircraft carriers ever built, was completed in 2016 for approximately $13 billion—companies such as Alion are tasked with finding better, faster, and cheaper ways to carry it out. The development of new designs and technologies is often not affordable, though, so instead “we emphasize leveraging ‘off-the-shelf’ solutions as a baseline for the project,” Samuelsen says. “We try to work with existing designs that can adapt to and accept newer features such as advanced radars.” It’s a technique and process for integrating modern capabilities into proven viable platforms that delivers the operational capability at lower development risk and lower costs.
One shipbuilder that Alion’s currently bidding to work with—for example, tasked with a significant project for the Royal Canadian Navy, the Canadian Surface Combatant (CSC)—is working through the Warship Designer and Combat Systems Integrator procurement to deliver an affordable, capable CSC. Development of the best-in-class vessel is being done using a military-off-the-shelf (MOTS) approach. “First-of-class designs have a higher cost, what we think of as ‘first article risk,’” Samuelsen says. “A MOTS approval significantly reduces the cost of engineering and construction by bringing forward proven and in-service designs.” Through the use of open design and architecture techniques, he adds, MOTS allows the introduction of such things as new radar and other components that are specific to the Canadian navy’s program.
But, how does an American company like Alion work for multiple countries? “We get permission from the US State and Defense Departments and work with Canada and Europe, which have their own rules, to ensure compliance” Samuelsen says. “It is complex, but it’s a matter of course for us.” The company, which maintains a strict vendor-neutral systems integrator position in the industry, is also careful to protect the intellectual property of the many vendors involved in each of its projects.
Ships are built in modules that get assembled at the customers’ launch sites. Alion provides input on how that assembly will take place and how different components will interact. Everyone collectively and ultimately bears responsibility for, well, smooth sailing.
Alion also supports national defense through network architecture and software engineering, systems engineering and integration, and equipment made for intelligence, surveillances and reconnaissance, and training. Samuelsen and his colleagues at Alion take a “vendor-agnostic” approach to systems selection and integration, focusing on how to “de-risk” the end product and ensure its adaptability over what could be a lifespan of more than 30 years in the case of ships. For Samuelsen, it’s all about delivering simple, elegant engineering solutions to Alion’s customers.
In image order: Courtesy of Wikipedia Creative Commons/ Dutch Ministry of Defence, Courtesy of USN / “The appearance of U.S. Department of Defense (DoD) visual information does not imply or constitute DoD endorsement,” Courtesy of Alion Science and Technology, Wikipedia Creative Commons/ Dutch Ministry of Defence, Courtesy of USN / “The appearance of U.S. Department of Defense (DoD) visual information does not imply or constitute DoD endorsement”
***
Damen’s portfolio is perfectly suited to today’s challenges. From fast interceptors and auxiliary vessels to very sophisticated combatants, from highly efficient coastguard vessels to state-of-the-art frigates and joint support ships. Striving to deliver the best, Damen has designed, built, and developed vessels for naval clients all over the world. www.damennaval.com