The design, construction, and ultimate functionality of a 450,000-square-foot warehouse that was converted into a Tier 3 data center and Tier 1 engineering research and development center ranks in the top tier of modern technological achievements. Without those whirring servers, fiber-optic cables, and networking equipment—collecting, processing, and sharing information—our lives could be thrown back to analog days.
But the key strategy with which Scott Krall and his team built the Durham Data Center and R&D Lab in Durham, North Carolina, had little to do with silicon chips and coaxial cables. The key to converting the existing warehouse building into a world-class facility that supports one of Dell EMC’s enterprise data centers and engineering labs in less than twelve months had more to do with human beings who worked together to achieve a common goal, who understood each other’s constraints and concerns, and who listened to the advice and input from all stakeholders involved on the project.

The team completed the project at 15 percent below the original budgeted value and earned a LEED Gold certification for commercial interiors as well. About two months into the design phase—and a month before construction began—Krall called together the team to define how they would work together by developing process approaches and commonly held project-performance objectives that would promote high performance.
“We had about 40 people in the room,” Krall, the director of construction services for Dell EMC, says. “The group included internal stakeholders, architects, engineers, general contractor DPR Construction, and key subcontractors. We wanted people to meet face to face, which is more productive than virtual meetings.”
Krall knows well the benefits of such meetings and how they impact building design. “Engineers have the design vision, but the contractors have the means and methods for delivering the most cost-effective, streamlined approach to accomplish the end result,” he says.
For example, with the Durham data center, the original plan was to incorporate the chiller plant within the building. Having the mechanical subcontractor involved early, they proposed fabricating a modular structure, manufactured off-site, to house those functions. “That helped free up valuable space within the building,” Krall says. “It also helped with the schedule, and because the structure was built off-site, there was less waste.”
This process of engaging the construction team early on with the design team stems from a similar experience Krall had in 1998. While working on an EMC project, the team was tasked with building a 650,000-square-foot manufacturing facility on a 13-month design and construction schedule, which meant a project team had to work under what Krall describes as a fast-track construction approach.
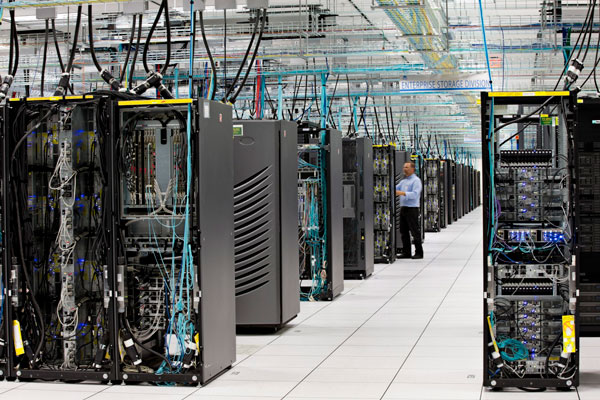
“One of the biggest challenges on fast-track projects is subcontractor coordination,” he says. A 3-D model-based process gives architecture, engineering, and construction professionals an improved, easy-to-understand way to efficiently plan, design, and construct buildings “With 3-D modeling, the team can sit around the table to virtually plan the means and methods on the constructability of the project,” Krall says. “It makes people accountable to each other, and it reduces change orders that might be due to conflicts encountered during construction.”
Overall, Krall’s process solidifies a sense of ownership. But, to underscore the human element in the mix of so much advanced technology, his project team members took a Myers-Briggs Type Indicator questionnaire at the beginning of the project. The MBTI is a respected tool based on Jungian theory that provides reference points for 16 personality types. Knowing one’s own type and that of others on a working team helps foster better working relationships, Krall says.
“Scott makes the process enjoyable,” says Greg Haldeman, a DPR Management committee member. “DPR knows that together we will build great things.”
That kind of grounding factored into what Krall refers to as the formal partnering session, a single-day event at the outset of the project. Led by a facilitator, each participant was asked to list what was important to him or her in the project. This helped develop common goals, communication protocols, project processes, roles, and responsibilities. “We established key milestones for the budget, schedule, and quality standards that were tracked throughout the project,” Krall says, detailing how the construction team was able to shorten lead times on purchasing equipment using a prepurchasing process.
Krall says that safety was another important goal established in the partnering session and that attention to accident prevention has other beneficial effects. “Safety means implementing comprehensive safety programs,” he says. “Having zero lost work days, all workers had ownership, ensuring that a safe work environment was maintained. And, having a clean work site led to enhanced productivity and better quality of the end product.”
That cleanliness mattered to the Durham project simply because it is a critical systems environment. Data centers and R&D labs not only need to house massive power demands and high heat loads; they must also adhere to strict maintenance protocols. The facility was renovated in two phases. The first phase encompassed building a structure within the existing building to support the mechanical and electrical systems for the data center and lab space. For the second phase, the team took what it learned from the first phase and removed all the internal structural elements and the roof, leaving only the perimeter walls. Then, it replaced the elements with a new internal structural system and roof, which allowed for more mechanical equipment on the roof. This approach yielded a substantial savings compared to the first phase.
In 2015, Dell Inc. acquired EMC in one of the largest deals ($67 billion) in tech history, according to Techcrunch.com. The company now relies more on outside providers, which changes the process a bit. What remains the same, though, is the quality of the product delivery, according to Krall. “Our internal customers expect a high level of quality and service to perform their work,” he says. That still comes from a highly sophisticated infrastructure, meticulously constructed and maintained, in structures—built by people.