Getting your Trinity Audio player ready...
|
U.S. Bank Stadium in Minneapolis is one of those buildings that stops you in your tracks. That’s not just because it’s a 1.75-million-square-foot football stadium. It’s an asymmetrical assemblage of trapezoids and triangles, interpreted by some as an abstract representation of a ship’s bow. Some simply regard it as an example of iconic yet functional architecture equipped with a roof sufficiently pitched to shed the city’s ample snowfalls.

In actuality, the stadium’s jagged apex is a reference to angular pieces of ice that accumulate below St. Anthony Falls, a series of waterfalls on the Mississippi River that meander through the Twin Cities. This was the intent of architects at Dallas-based HKS, a firm that has several stadiums in its portfolio.
Get a little closer to the stadium on game days and, weather permitting, five Paul Bunyan-worthy doors—each 55 feet wide and ranging from 75 to 95 feet tall—gape to the open position. The multipurpose venue opened for business in 2016 and proves function can rival form. It hosts about 300 events per year while managing to earn high scores for sustainability: Since June 2018, it’s diverted over 1,500 tons of compost and recycling material from the waste stream.
Director of Operations Curtis Schmillen has a special perspective on how U.S. Bank Stadium actually “lives,” as he describes it. He was hired to work for the stadium’s operator, ASM Global, after overseeing the MEP/T (mechanical, electrical, plumbing, and technology) design and construction as it was being built. In other words, he knows exactly what’s behind the walls.
“When managing a facility, the scope increases from just pipe, conduit, and concrete to include user experience, utilization, and consumption,” says Schmillen, who explains that once people enter the building, they bring in their body temperature, breathe the air, consume food, use the restroom, access the Wi-Fi, and throw away garbage. “Buildings are dynamic—living, breathing entities.”
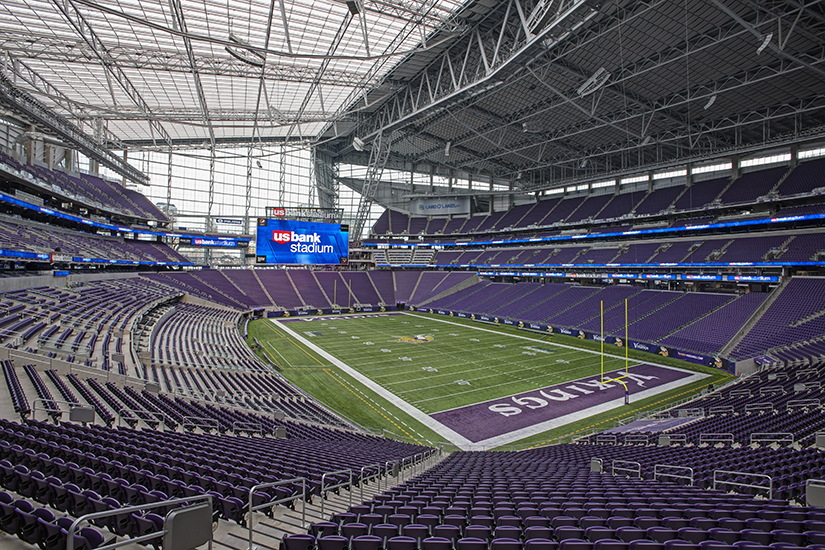
Schmillen says the transition from being a builder to a facility manager was relatively seamless. “The principles that make you successful at managing construction projects apply to managing a facility,” he says. One big difference is deadlines. In construction, the delivery of both the completed project and the milestones leading up to that date are well defined. Managing the facility is different. “Your focus turns from brick-and-mortar to the environment in and around the space. What do people need, what does equipment need, and what makes the space comfortable?”
The roof of the stadium was a big point of consideration in its design, a matter of reconciling the desire for an open-air stadium against the economic imperative to host other events, like concerts or trade shows, year-round. Given the Minneapolis climate (54 inches of snow per year, most of that in December, January, and February), some type of roof would be necessary. Retractable roofs have been popular at other stadiums built in the 21st century, but cost estimates exceeded the project’s $1.1 billion budget.
The solution was a “clear roof,” essentially a window to the sky. About 240,000 square feet of a special type of material—a three-layered ETFE (ethylene tetrafluoroethylene), which is lighter and stronger than traditional roofing materials—cover 60 percent of the roof. Set asymmetrically to favor southern exposure, it brings in maximal daylight, while a 1:12 roof pitch guides snow to a melting system that prevents snow buildup. In fact, US Bank Stadium replaced the former Hubert H. Humphrey Metrodome, which had an air-supported fiberglass fabric roof that collapsed in 2010 from an 18-inch snowfall.
The ETFE roof creates an outdoor feel that is so effective, “you can literally see clouds and planes overhead as you look up toward the sky,” Schmillen says. “Especially on those sunny days in winter when there is snow on the ground and the temperature is below freezing, walking down onto the field feels like you are outside on a nice spring day.”
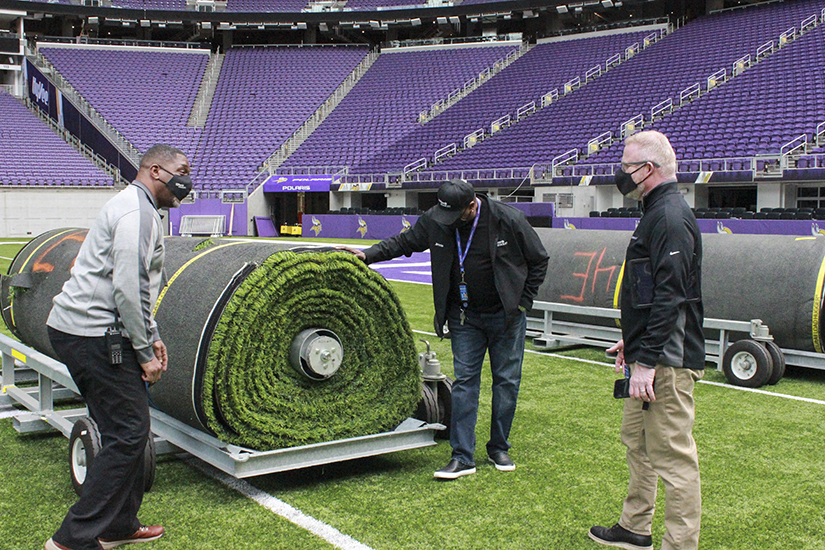
The feeling of being outside is aided as well by those huge doors, which cumulatively consist of 30,000 square feet of glass (and weigh 40,000 tons). A first of its kind in the NFL, as other stadium entrances slide laterally, U.S. Bank Stadium’s doors pivot on a brass ring around a reinforced steel column. The doors required some tricky engineering and more than a little courage to build. “The doors are a magnet for fans and first-time stadium attendees,” Schmillen says. “Watching these doors open before a Vikings game, with the crowds on the plaza outside, is a spectacle that must be seen.”
The doors can’t be used in bad weather—human-scale doors at the bottom are then employed—but Schmillen is surprised how infrequently that matters.
U.S. Bank Stadium hosted the 2018 Super Bowl, achieving another first. The team diverted over 90 percent of waste to recycling, energy recovery, and composting, making it the inaugural legacy project for a Zero Waste Super Bowl. It bears mentioning that Minneapolis has impressive green infrastructure with electricity-generating incineration, recycling, and a commercial composting facility, plus 100 miles of bikeways (this was the first stadium to be Bicycle Friendly Business-certified, with over 180 bike racks). By 2019, the stadium also became the first professional sports stadium to earn LEED Platinum certification for operations and maintenance using the arc performance platform, attributable in part to an air purification system (AtmosAir Solutions) that also reduces energy consumption.
“U.S. Bank Stadium is one of the most innovative and forward-looking sports venues in the world, and we are proud to work with Curtis and their team to help bring people back together safely,” says Steve Levine, president and CEO of AtmosAir Solutions. “Bipolar ionization is an important layer to combating airborne pathogens and will help fans enjoy their football or concert experiences with additional confidence and peace of mind.”
In addition, Schmillen oversees the stadium’s cleaning services team and has been instrumental in the implementation of ASM Global’s environmental health and safety program, VenueShield. The program was developed in partnership with leading medical professionals, industry experts, and public health officials in response to the COVID-19 pandemic. VenueShield focuses on six core components: environmental hygiene, the customer journey, workforce safety, food safety, technology, and public awareness.
For a city known for the months that it’s blanketed in white, US Bank Stadium stands out proudly by offering a vibrant shock of green.
Gephart Electric and Low Voltage Systems congratulates Curtis on this well-deserved recognition. It has been a pleasure working with him through the initial facility construction and the maintenance and improvements required for a facility like U.S. Bank Stadium. His dedication and leadership create a great working environment and team.