Getting your Trinity Audio player ready...
|
The owners of CambridgeSide mall, located just across the Charles River from Boston and close to Harvard University, hoped to convert their empty retail spaces to offices. The evolution from brick-and-mortar to online shopping already challenged the property owner, but the pandemic and work-from-home era put a crimp on even those stores-to-office plans. Instead, companies are contracting, not expanding, their office footprints.
But Saquib Butt, senior vice president of infrastructure and assets for SmartLabs, and his team are helping launch a new idea: convert the third floor of the mall, about 175,000 square feet, into scientific lab space. SmartLabs is a laboratory-as-a-service leader, meaning it designs, builds, and operates integrated, enterprise-grade research environments. The organization largely serves pharma research firms that find renting such facilities to be smarter economics under certain circumstances.
Butt oversees the full development of sites for the company, which currently has five such facilities operating or under construction in Philadelphia, Greater Boston, and the Bay Area in San Francisco. “We know Boston well, including its markets and submarkets,” Butt says. In fact, the company itself is based in Boston. The location provides a strategic advantage given the number of sciences companies based in Massachusetts, including Boston Scientific and Sanofi (formerly Genzyme) where Butt worked for almost 20 years in a related capacity.
“I’d like to think I’m good at assembling a team of personalities that work well together, which is a key in any big initiative or project undertaking.”
Saquib Butt
In his job with SmartLabs, Butt ensures buildings have the proper floor heights, column spacing, air handling capacities, and more than a dozen other features that are required for pharmaceutical research and manufacturing.
Biomedical research facilities also require animal care facilities (ACF) programs, which is the mid-stage testing portion of pharmaceutical development. Taking up about 10 to 12 percent of floor space in the typical SmartLabs operation, an ACF program has to meet strict federal codes as determined by the National Institutes of Health. These include “fostering a steady-state existence in which they [animals which are usually rodents] are subjected to minimal stress and environmental fluctuations,” according to Management of Animal Care and Use Programs in Research, Education, and Testing, 2nd edition.
“Air circulation is handled separately from the rest of the facility, and provides special lighting for different times of day,” Butt explains.
Facilities that host pharmaceutical research also need to handle emissions and waste according to highly regulated codes. For example, air exhaust must go through a filtration process. “California codes are also more stringent,” Butt says. “It includes filtering out carbon emissions, and those same codes are coming to the Boston area.” He is also confident that having facilities in the Bay Area equips them with the know-how to achieve these higher standards.
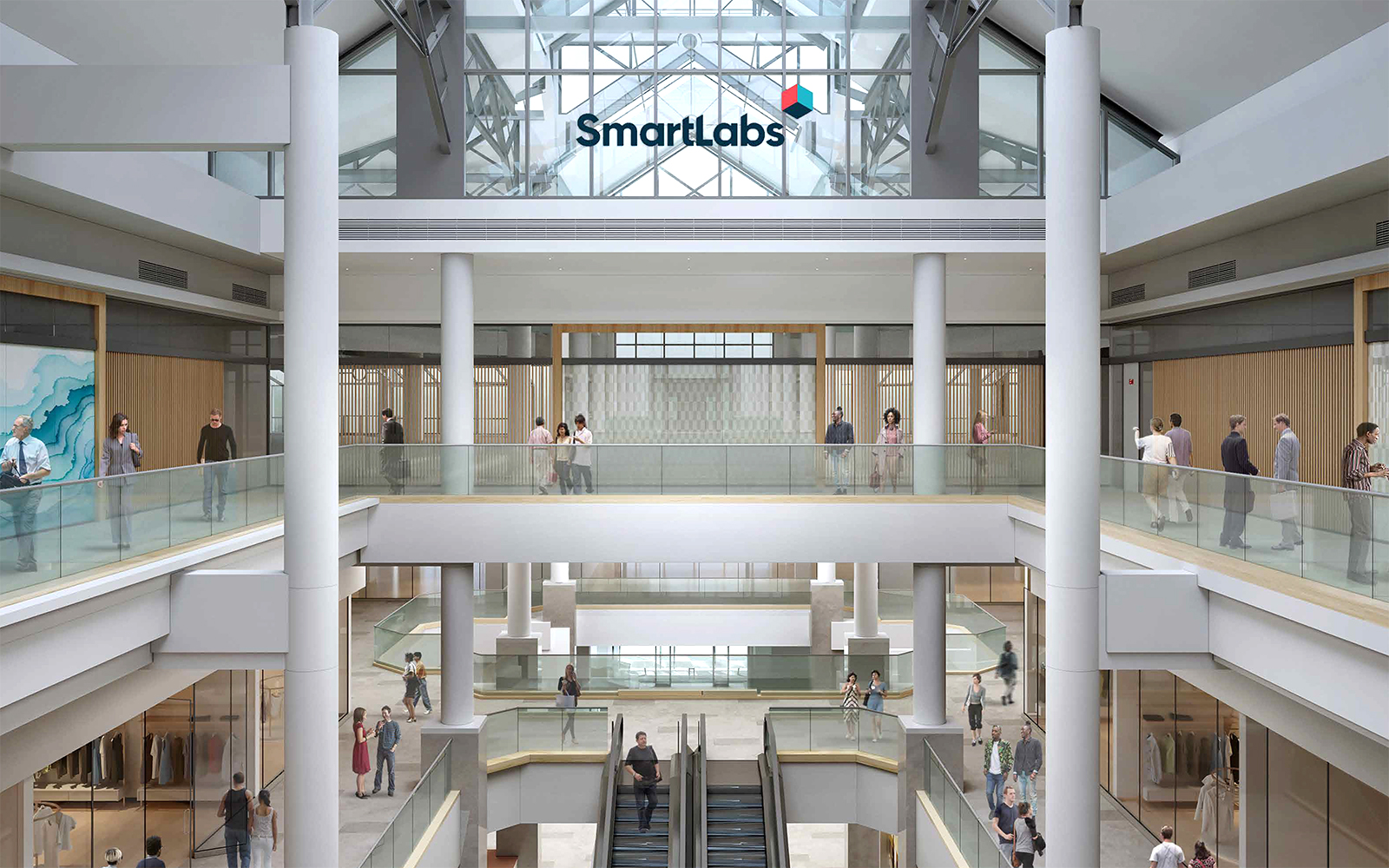
Where wastewater is involved, all research effluent has to be treated before entering the municipal waste system. That includes ensuring all fluids are at the neutral, level 7 PH balance. Biowaste goes through a bio-kill system, says Butt, using chemicals, steam, and electricity to kill microorganisms.
These are the kinds of features that Butt’s team of in-house architects and engineers have to design into former shopping malls and other facilities. They also build from the ground up, where the economics make that the better choice. “We have a unique design format, based on a universal lab framework,” he says. “But it varies by location. It’s always our preference to build new versus retrofits.”
His primary responsibility is to ensure the entire infrastructure—including facility functionality, location that attracts talent and clients, reliable utilities, plus the economics of the build in juxtaposition with revenues it will achieve—works.
“Having worked with Saquib on several project over the years, I have come to appreciate his deep technical knowledge and positive attitude towards challenges,” says Mike Jackson, senior vice president at Truebeck Construction. “By pairing those skills, he is remarkably successful at consistently achieving great results. I am proud to be one of his trusted partners.”
Evolving pharma research and production—and unplanned events—also throw some curves in facilities design. “Changes can be subtle and slow,” Butt explains. “About 15 years ago, we used huge stainless steel bioreactors that had to be thoroughly cleaned between uses. Today, we have single-use disposable bags that enables faster turnover in production.”
“About 15 years ago, we used huge stainless steel bioreactors that had to be thoroughly cleaned between uses. Today, we have single-use disposable bags that enables faster turnover in production.”
Saquib Butt
Novel drugs have their own demands, and the mass-production of the COVID-19 vaccines required a ramped up, high-volume process. Another innovation is CAR T cell therapy, a blood cancer immunotherapy treatment where an individual patient’s blood is engineered in the lab to fight the cancer, then reinjected into the patient. The labs have a designated area for this relatively new, breakthrough process. SmartLabs infrastructure is designed to cater to those biotherapeutics research needs for an advanced flexible space to conduct research and testing.
Seismic and climatological events have to be planned, as well. These facilities have backup generators for extended power shortages, but even a few seconds of lost power can be disastrous. For this reason SmartLabs designs an uninterrupted power supply system that ensures air exchangers, air pressure, humidity, and temperatures are constant to keep the valuable research and production activities going seamlessly.
Butt recognizes the evolving nature of the spaces he oversees and feels his working team is an essential part of it. “I’d like to think I’m good at assembling a team of personalities that work well together, which is a key in any big initiative or project undertaking,” he says.