|
If Matt Knipstein had started working in his capacity as senior director of campus facilities and maintenance for Sweetwater Sound back when the company launched in 1979 in Fort Wayne, Indiana, his responsibilities would have included one groovy Volkswagen microbus and a garage recording studio.
That’s not what happened, of course. Knipstein joined the online retailer of musical instruments and sound equipment in 2015, initially as director of mechanical operations, when the company had about 1,000 employees. Since then, that number has grown to 3,000 people working in various capacities across six buildings that include a 40,000-square-foot retail store, a 750,000-square-foot distribution center, administrative offices, a gym, racquetball courts, and a food court that welcomes employees and townspeople alike. In addition, its media center and recording facility have been used in the flesh by Dolly Parton, Kenny Rogers, Stevie Wonder, Charlie Daniels, Guns N’ Roses’ Slash, Buddy Guy, ZZ Top, Vince Gill, among others.
Celebrities visit Sweetwater to test out some of the 34,000 guitars and other instruments as well as sound equipment at any given time. It speaks to the place that the company, which is the largest supplier of musical instruments in the country, holds in the music industry.
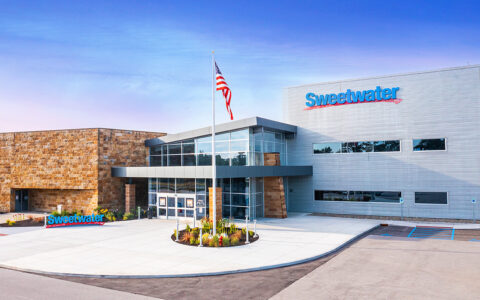
Accommodating customers is part of Knipstein’s job, as the construction, upkeep, and functionality of buildings and building systems can make or break the operation. But the employees are Knipstein’s top priority. This is a workplace where, as one might imagine, music is in their veins. While Knipstein isn’t a musician himself, that puts him in the minority. “Most everyone here has a love for music,” he says. “Music is how we remember our lives. I love the art of music, and we are fortunate to work where musical dreams come true.”
Knipstein says the company culture stems from its founder, Chuck Surack. He was a musician, traveling in that original microbus, who decided to stop touring and instead offer recording services. The company grew organically and through acquisitions—earning “fastest-growing companies” status in Inc. in 1993, 1994, and 1995—and accelerating at a quicker pace with the advent of online sales in the late 1990s.
“Music is how we remember our lives. I love the art of music, and we are fortunate to work where musical dreams come true.”
Matt Knipstein
The Sweetwater campus buildings are not ordinary structures. A single eight-string electric guitar (Strandberg Boden) sells for about $3,600 from Sweetwater, while an electronic stage piano (Nord Piano 5) retails at $3,000, and a brass instrument from their newly acquired band and orchestra line can be worth as much as $7,700 (Yamaha professional double French horn). Strict temperature and humidity controls are essential in warehousing and shipping operations to protect the valuable instruments.
“We have an automated system and mechanical technician who get notifications if the air temps or humidity are off,” says Knipstein. The buildings where the instruments are housed have massive diesel generators in case of power outages.
Speaking of power, the company has recently installed no less than 900 solar panels (covering 93,000 square feet), a 1-MW system that annually displaces the carbon equivalency of burning 79,000 gallons of gasoline. Sweetwater also lays claim to the first LEED Platinum building in Indiana, with bamboo flooring, ample windows for natural light, and automated controls that adjust electric lighting according to sunshine, cloudiness, and nighttime.
“We live by an idea we call ‘Sweetwater Time,’ which is about our focus on customer service.”
Matt Knipstein
Knipstein’s role in creating these green features is no less important than the ongoing maintenance of existing facilities. His own staff of about 40 people tends to janitorial functions plus electrical, mechanical, and light construction—including maintenance of fiber-optic equipment essential to the data and voice technologies on which their approximately 800 customer service representatives (and thousands of customers) depend on every day.
“We live by an idea we call ‘Sweetwater Time,’ which is about our focus on customer service,” notes Knipstein. “For my team, the customers are our employees.”
As just one example of what that looks like, Sweetwater’s food operations feed 2,000 people daily from two kitchens. That’s breakfast, lunch and dinner, six days a week, with 42 food-service personnel. In fact, the company offers “Cheeseburger Thursdays” and pizza dough is made from scratch. Employee meals are subsidized (customers from outside the company pay full price) and the facility operates in a break-even cost-revenue structure. These food operations must meet health codes, which depend on functioning refrigeration and cooking equipment, as well as clear drain lines and sanitary garbage disposal. If Knipstein’s maintenance program were to fail, that could mean 2,000 hungry people.
That hasn’t happened, fortunately. Sweetwater’s role in the Fort Wayne community is an important part of what it does; the company is also a major contributor to area charities, particularly in the arts and music sector.All of that wouldn’t be possible, though, without well-designed and maintained facilities—much of it just as hip as a musician’s mid-century microbus.