Greg Thomas’s path to healthcare was a long and winding one. Currently the division vice president of developmental construction projects at Kindred Healthcare in Louisville, Kentucky, Thomas’s story began out west, while he was studying engineering.
“I graduated from the University of Colorado with a civil engineering degree,” he recalls. “But, before that, I went to a college called LeTourneau College—now LeTourneau University—in Longview, Texas, where I studied mechanical engineering technology. After I graduated from Colorado, I worked in Denver with the Regional Transportation District, where at the time they were building a district shop for bus repairs.”
Although he got his start in Denver, it wasn’t long before he left. An old acquaintance connected with him and “told me to come out to Louisville and work with him on a development that he was planning,” Thomas recalls. “I thought, ‘This’ll be great. I’ll go out and work for him and grow in the development side of the business,’ which I really wanted to do. So, I packed up my bags and moved from Colorado at age 28, out to Louisville to start working for him.”
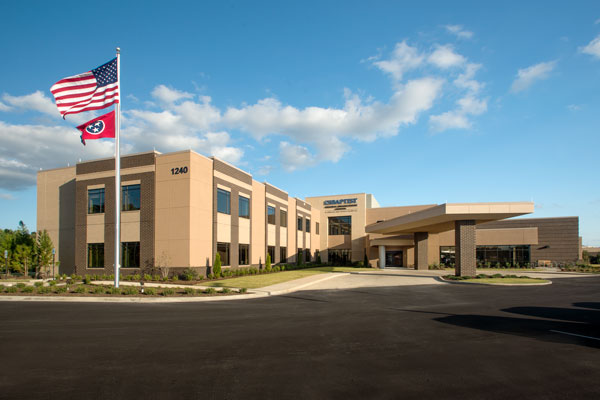
Everything In Its Right Place
Thomas spent his first 20 years in Louisville as a general contractor and manager of a concrete slipform company and at the Ford Motor Company Kentucky Truck Plant, flexing his mechanical engineering chops. As a construction manager, he oversaw a 200-acre development in Jefferson county, one of the largest in the county at the time. Then, in 2007, he got the opportunity to work at Kindred Healthcare.
For his first nine years at Kindred, Thomas oversaw the design and construction of long-term acute-care hospitals, which required operating rooms, intensive-care units, and radiology departments. He also began implementing new design initiatives for Kindred’s new Transitional Care Center buildings.
“I, along with a developer, created a model building for our transitional care centers,” Thomas says. “By designing a building using a model, we were able to keep the core of the building relatively unchanged and only had to adjust our layouts to compensate for bed counts and different land configurations.”
Kindred’s model buildings revolve around several core design elements such as a typical patient-room layout; locations of support spaces such as pharmacies, labs, nurse’s stations, kitchens, and administrative offices; and common-size therapy spaces with standardized equipment. These buildings tend to be of a similar shape, with standardized equipment and furniture, but it’s important to note that each of these buildings is unique in its own ways, with interior finish selections and exterior material and color choices. Model buildings also still need to be adjusted to meet variable patient needs, functional programs, and local code requirements—including ensuring their HVAC systems are appropriate for each hospital’s climate. Thomas’s move toward model buildings expanded. Not long after, Kindred acquired a company that had designed a model building for its inpatient rehab facilities.
“We acquired a company with outstanding development leadership that also had a model building that it had been using effectively to meet its program and needs,” Thomas says, “and we wanted to continue to grow by utilizing those same design expectations it’d operated by.”
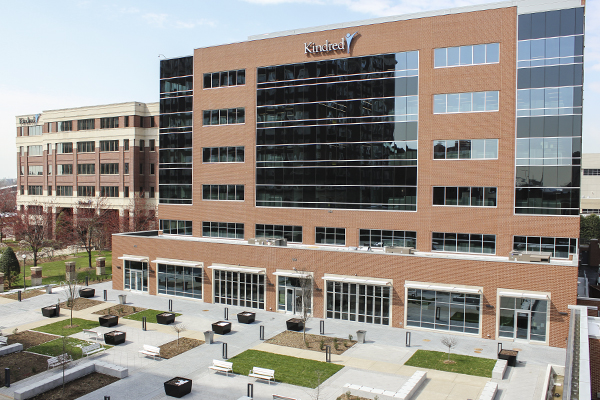
The Kindred Support Center
Currently, Thomas’s biggest project has been overseeing a new addition for Kindred’s Support Center in Louisville proper. “The new addition to the Support Center was a lot of fun to build,” Thomas says, “because it wasn’t a hospital. It was something different and challenged me to coordinate a variety of construction detail in a busy office environment. It engaged a good group of architects who led the way on designing and integrating a new, modern building onto our older, existing facility.”
The project was also very enjoyable because it was at Thomas’s office. He could walk down to the construction site, making it easy to for him to be involved and engaged with the contractors on a daily basis. It’s also one of Kindred’s tallest construction project to date, at six stories, outpacing its previous largest construction—a hospital—by three.
“What I enjoy about all the projects I work on,” Thomas says, “is that there’s not a single site that’s the same. I’m a trained civil engineer, so I enjoy the variations you get from job to job. There’s challenges and different design requirements related to the site work and layout.”
Kindred Healthcare’s Renovations and New Constructions
Throughout his time at Kindred Healthcare, Greg Thomas has overseen a number of unique and interesting projects simultaneously. He shares some of the most exciting ones below.
Kindred Hospital (Melbourne, FL): “That was my first building, built to withstand hurricane conditions. Early on in the project, we actually got hit by Hurricane Faye, but luckily we were in the early stages of the project, so we didn’t have too much damage. You can land at the Melbourne Airport and be at that location within five minutes—it’s right on their property.”
Kindred Hospital (Seattle): “This particularly challenging hospital project, located on a hill in the city, was a renovation of a concrete structure with low floor-to-ceiling clearances. New rooftop HVAC systems were installed, with ductwork running to each floor, down the outside of the building, and through shafts creatively designed to architecturally enhance the exterior appearance of the building. We also constructed a large underground electrical-transformer vault beneath the building portico and connected an entrance through the basement.”
Mercy Rehabilitation Hospital (Des Moines, IA): “The part I welcomed the most was that this was a model building, so there wasn’t a need to go through a lot of hoops with our user groups and design meetings ahead of starting construction, like you would in another case.”
Photos: Courtesy of Kindred Healthcare